



Date:03/08/18
One of the biggest challenges facing 3D printing is the ability to print in full, highly detailed color. However, not all 3D printing technologies, such as selective laser sintering (SLS) and stereolithography (SLA), are able to print directly in color. Researchers at The Institute of Photonic Sciences (IFCO) in Spain have recently developed a faster and cost-effective 3D printing method that can print objects in all the colors. Their results is published in the ACS journal Nano Letters.
Selective laser sintering (SLS) printers uses a laser as the power source to sinter specific regions of a powdered material, typically nylon or polyamide, to form a solid 3D structure. Once the first layer has completed the build platform/part bed drops by a pre-set amount. Then another layer of material is put down, and the second cross-section is fused directly on top of it. This continues until every cross-section has been laid and fused.
Over the past years, the use of photothermal sensitizers to facilitate the sintering of polymer powders is becoming more common. To reduce the energy requirements of the process, researchers have added compounds called photosensitizers to the polymer powders. These materials, such as carbon nanotubes, carbon black and graphene, absorb light much more strongly than the polymers and transfer heat to them, enabling the use of cheaper, lower-power lasers.
However, the carbon-based photosensitizers can only produce printed objects that are gray or black. To create white or colorful prints with this method, visibly transparent equivalents are needed. Gerasimos Konstantatos, Romain Quidant and their coworkers at IFCO wanted to find a photosensitizer that would enable color printing by the SLS 3D printing method.
“To create white or colorful prints with this method, visibly transparent equivalents are needed. Here, we address this problem by designing resonant photothermal sensitizers made of plasmonic nanoparticles that strongly absorb in the near-infrared, while only minimally interacting with visible light,” the researchers state.
To create stable colorful nanocomposite powders, gold nanorods were coated with silica before being mixed with polyamide powders. At resonance, according to the researchers, these composites showed greatly improved light-to-heat conversion compared with equivalent composites using the industry standard carbon black as a sensitizer and could be sintered using low-power light sources. Furthermore, the new photosensitisers could also produce much whiter and – when mixed with dyes – brightly coloured 3D objects.
Importantly, the materials are cost-effective for large-scale production, researchers said. They have filed several patent applications related to the new technology.
“Our results open a new route to utilize plasmonic nanoparticles to produce colorful and functional 3D-printed objects,” the researchers explain. They presented their research in a paper entitled “White and Brightly Colored 3D Printing Based on Resonant Photothermal Sensitizers.”
New photosensitizers help overcome color limitations in SLS 3D printing
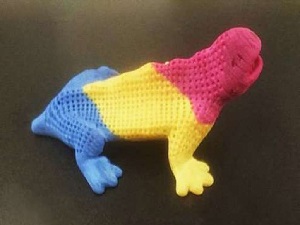
Selective laser sintering (SLS) printers uses a laser as the power source to sinter specific regions of a powdered material, typically nylon or polyamide, to form a solid 3D structure. Once the first layer has completed the build platform/part bed drops by a pre-set amount. Then another layer of material is put down, and the second cross-section is fused directly on top of it. This continues until every cross-section has been laid and fused.
Over the past years, the use of photothermal sensitizers to facilitate the sintering of polymer powders is becoming more common. To reduce the energy requirements of the process, researchers have added compounds called photosensitizers to the polymer powders. These materials, such as carbon nanotubes, carbon black and graphene, absorb light much more strongly than the polymers and transfer heat to them, enabling the use of cheaper, lower-power lasers.
However, the carbon-based photosensitizers can only produce printed objects that are gray or black. To create white or colorful prints with this method, visibly transparent equivalents are needed. Gerasimos Konstantatos, Romain Quidant and their coworkers at IFCO wanted to find a photosensitizer that would enable color printing by the SLS 3D printing method.
“To create white or colorful prints with this method, visibly transparent equivalents are needed. Here, we address this problem by designing resonant photothermal sensitizers made of plasmonic nanoparticles that strongly absorb in the near-infrared, while only minimally interacting with visible light,” the researchers state.
To create stable colorful nanocomposite powders, gold nanorods were coated with silica before being mixed with polyamide powders. At resonance, according to the researchers, these composites showed greatly improved light-to-heat conversion compared with equivalent composites using the industry standard carbon black as a sensitizer and could be sintered using low-power light sources. Furthermore, the new photosensitisers could also produce much whiter and – when mixed with dyes – brightly coloured 3D objects.
Importantly, the materials are cost-effective for large-scale production, researchers said. They have filed several patent applications related to the new technology.
“Our results open a new route to utilize plasmonic nanoparticles to produce colorful and functional 3D-printed objects,” the researchers explain. They presented their research in a paper entitled “White and Brightly Colored 3D Printing Based on Resonant Photothermal Sensitizers.”
Views: 714
©ictnews.az. All rights reserved.Similar news
- The mobile sector continues its lead
- Facebook counted 600 million active users
- Cell phone testing laboratory is planned to be built in Azerbaijan
- Tablets and riders outfitted quickly with 3G/4G modems
- The number of digital TV channels will double to 24 units
- Tax proposal in China gets massive online feedback
- Malaysia to implement biometric system at all entry points
- Korea to build Green Technology Centre
- Cisco Poised to Help China Keep an Eye on Its Citizens
- 3G speed in Azerbaijan is higher than in UK
- Government of Canada Announces Investment in Green Innovation for Canada
- Electric cars in Azerbaijan
- Dominican Republic Govt Issues Cashless Benefits
- Spain raises €1.65bn from spectrum auction
- Camden Council boosts mobile security