



Date:08/08/18
Researchers from Harvard’s Wyss Institute for Biologically Inspired Engineering and John A. Paulson School of Engineering and Applied Sciences (SEAs), as well as Boston University have teamed up to create the first small-scale, multi-flexible robot. While multi-flexible robots have been developed, it has been impossible to create these robots at the small scale, until now.
The research team created an integrated fabrication process that allows for the development of soft-robotics at the millimeter scale with micro-meter features. With the new process, the team has created a robotic soft spider that was inspired by the Australian peacock spider. The tiny robot was made with a single elastic material with body-shaping motions and color features.
"The smallest soft robotic systems still tend to be very simple, with usually only one degree of freedom, which means that they can only actuate one particular change in shape or type of movement," said Sheila Russo, Ph.D., co-author of the study. "By developing a new hybrid technology that merges three different fabrication techniques, we created a soft robotic spider made only of silicone rubber with 18 degrees of freedom, encompassing changes in structure, motion and color, and with tiny features in the micrometer range."
"In the realm of soft robotic devices, this new fabrication approach can pave the way towards achieving similar levels of complexity and functionality on this small scale as those exhibited by their rigid counterparts. In the future, it can also help us emulate and understand structure-function relationships in small animals much better than rigid robots can," she continued.
The new device is called Microfluidic Origami for Reconfigurable Pneumatic Hydraulic (MORPH) devices. A soft lithography technique is used to generate 12 layers of elastic silicone to create the soft material base of the spider. Each layer is cut out of a mold with a laser micromachining technique. The layers were then bonded together to create the 3D structure of the soft spider robot. A network of hollow microfluidic channels that were integrated into each layer.
A technique called injection-induced self-folding pressurized one set of the integrated microfluidic channels with a curable resin. This creates individual layers that bend into the final configuration and fixed space when the resin hardens.
"We can precisely control this origami-like folding process by varying the thickness and relative consistency of the silicone material adjacent to the channels across different layers or by laser-cutting at different distances from the channels. During pressurization, the channels then function as actuators that induce a permanent structural change," said first and corresponding author Tommaso Ranzani, Ph.D.
The final set of microfluidic channels in the robot act as actuators. The actuators give the eyes and the body of the robot color — the same color as the real Australian peacock spider. The actuators are key to starting the walking motions in the spider robot’s legs.
"This first MORPH system was fabricated in a single, monolithic process that can be performed in a few days and easily iterated in design optimization efforts," said Ranzani.
"The MORPH approach could open up the field of soft robotics to researchers who are more focused on medical applications where the smaller sizes and flexibility of these robots could enable an entirely new approach to endoscopy and microsurgery," said Wyss Institute founding director Donald Ingber, M.D., Ph.D., who is also a professor of bioengineering at SEAS.
The paper on this new spider robot was published in Advanced Materials.
First Multi-Flexible Robot Inspired by Australian Spider
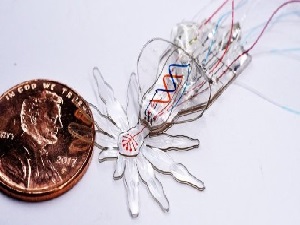
The research team created an integrated fabrication process that allows for the development of soft-robotics at the millimeter scale with micro-meter features. With the new process, the team has created a robotic soft spider that was inspired by the Australian peacock spider. The tiny robot was made with a single elastic material with body-shaping motions and color features.
"The smallest soft robotic systems still tend to be very simple, with usually only one degree of freedom, which means that they can only actuate one particular change in shape or type of movement," said Sheila Russo, Ph.D., co-author of the study. "By developing a new hybrid technology that merges three different fabrication techniques, we created a soft robotic spider made only of silicone rubber with 18 degrees of freedom, encompassing changes in structure, motion and color, and with tiny features in the micrometer range."
"In the realm of soft robotic devices, this new fabrication approach can pave the way towards achieving similar levels of complexity and functionality on this small scale as those exhibited by their rigid counterparts. In the future, it can also help us emulate and understand structure-function relationships in small animals much better than rigid robots can," she continued.
The new device is called Microfluidic Origami for Reconfigurable Pneumatic Hydraulic (MORPH) devices. A soft lithography technique is used to generate 12 layers of elastic silicone to create the soft material base of the spider. Each layer is cut out of a mold with a laser micromachining technique. The layers were then bonded together to create the 3D structure of the soft spider robot. A network of hollow microfluidic channels that were integrated into each layer.
A technique called injection-induced self-folding pressurized one set of the integrated microfluidic channels with a curable resin. This creates individual layers that bend into the final configuration and fixed space when the resin hardens.
"We can precisely control this origami-like folding process by varying the thickness and relative consistency of the silicone material adjacent to the channels across different layers or by laser-cutting at different distances from the channels. During pressurization, the channels then function as actuators that induce a permanent structural change," said first and corresponding author Tommaso Ranzani, Ph.D.
The final set of microfluidic channels in the robot act as actuators. The actuators give the eyes and the body of the robot color — the same color as the real Australian peacock spider. The actuators are key to starting the walking motions in the spider robot’s legs.
"This first MORPH system was fabricated in a single, monolithic process that can be performed in a few days and easily iterated in design optimization efforts," said Ranzani.
"The MORPH approach could open up the field of soft robotics to researchers who are more focused on medical applications where the smaller sizes and flexibility of these robots could enable an entirely new approach to endoscopy and microsurgery," said Wyss Institute founding director Donald Ingber, M.D., Ph.D., who is also a professor of bioengineering at SEAS.
The paper on this new spider robot was published in Advanced Materials.
Views: 633
©ictnews.az. All rights reserved.Similar news
- The mobile sector continues its lead
- Facebook counted 600 million active users
- Cell phone testing laboratory is planned to be built in Azerbaijan
- Tablets and riders outfitted quickly with 3G/4G modems
- The number of digital TV channels will double to 24 units
- Tax proposal in China gets massive online feedback
- Malaysia to implement biometric system at all entry points
- Korea to build Green Technology Centre
- Cisco Poised to Help China Keep an Eye on Its Citizens
- 3G speed in Azerbaijan is higher than in UK
- Government of Canada Announces Investment in Green Innovation for Canada
- Electric cars in Azerbaijan
- Dominican Republic Govt Issues Cashless Benefits
- Spain raises €1.65bn from spectrum auction
- Camden Council boosts mobile security