



Date:13/09/17
3D printing technology has shown its usefulness in a number of applications, but few sectors have benefited like the aerospace industry. The development process for rocket engines is being rejuvenated by additive manufacturing, allowing for faster, more complex production. In the past, we’ve seen 3D printed rocket testing undertaken by the likes of NASA and MIT, and now Australian researchers are joining these prestigious ranks.
Engineers from Monash University and the school’s spin-out company Amaero recently partnered up for Project X. In this collaborative effort, the team designed, 3D printed, assembled, and tested an aerospace rocket engine in just four months.
The rocket has an “aerospike” design, contributing a bell-shaped configurations that is different from most other rocket models. This type of engine works by firing gases along a spike and using atmospheric pressure to create a virtual bell. The unique shape of the spike allows for higher efficiency at higher altitudes. However, the complex shape is difficult to produce with traditional manufacturing processes, which is where 3D printing comes into play.
But the most impressive aspect of Project X is the four month time period it took to 3D print and successfully test the jet engine rocket. According to the Monash University researchers, 3D printing technology helped speed up the production process and also enhance the overall performance of the rocket.
“We were able to focus on the features that boost the engine’s performance, including the nozzle geometry and the embedded cooling network. These are normally balanced against the need to consider how on earth someone is going to manufacture such a complex piece of equipment. Not so with additive manufacturing,” says Graham Bell, the NextAero project lead.
Two years ago, Monash University researchers became the first in the world to 3D print a jet engine. This led the engineering team to found Amaero, an additive manufacturing specialist that is winning contracts with major aerospace companies. The company enables Australian companies to design, 3D print, and test metal components. The 3D printing specialist services clients in many fields, from aerospace to medical.
Now, with the success of Project X, the team has launched another venture called NextAero. They plan to take their new concepts to the International Astronautical Congress in Adelaide later this month.
3D Printed Aerospace Rocket Engine Successfully Tested by Australian Engineers
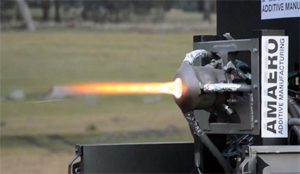
Engineers from Monash University and the school’s spin-out company Amaero recently partnered up for Project X. In this collaborative effort, the team designed, 3D printed, assembled, and tested an aerospace rocket engine in just four months.
The rocket has an “aerospike” design, contributing a bell-shaped configurations that is different from most other rocket models. This type of engine works by firing gases along a spike and using atmospheric pressure to create a virtual bell. The unique shape of the spike allows for higher efficiency at higher altitudes. However, the complex shape is difficult to produce with traditional manufacturing processes, which is where 3D printing comes into play.
But the most impressive aspect of Project X is the four month time period it took to 3D print and successfully test the jet engine rocket. According to the Monash University researchers, 3D printing technology helped speed up the production process and also enhance the overall performance of the rocket.
“We were able to focus on the features that boost the engine’s performance, including the nozzle geometry and the embedded cooling network. These are normally balanced against the need to consider how on earth someone is going to manufacture such a complex piece of equipment. Not so with additive manufacturing,” says Graham Bell, the NextAero project lead.
Two years ago, Monash University researchers became the first in the world to 3D print a jet engine. This led the engineering team to found Amaero, an additive manufacturing specialist that is winning contracts with major aerospace companies. The company enables Australian companies to design, 3D print, and test metal components. The 3D printing specialist services clients in many fields, from aerospace to medical.
Now, with the success of Project X, the team has launched another venture called NextAero. They plan to take their new concepts to the International Astronautical Congress in Adelaide later this month.
Views: 323
©ictnews.az. All rights reserved.Similar news
- Azerbaijani project to monitor disease via mobile phones
- Innovative educational system to be improved under presidential decree
- NTRC prolongs license of two TV and radio organizations for 6 years
- Azerbaijan establishes e-registry for medicines
- Azerbaijani museum introduces e-guide
- Nar Mobile opens “Nar Dunyasi” sales and service center in Siyazan city
- International conference on custom electronic services held in Baku
- OIC secretary general to attend COMSTECH meeting in Baku
- Azerbaijan develops earthquake warning system
- New law to regulate transition to digital broadcasting in Azerbaijan
- Azerbaijani State Social Protection Fund introduces electronic digital signature
- Intellectual traffic management system in Baku to be commissioned in December
- Tax Ministry of Azerbaijan started receiving video-addresses
- World Bank recommends Azerbaijan to speed up e-service introduction in real estate
- Azerbaijan to shift to electronic registration of real estate