



Date:01/02/19
Software developer Gal Shaul, along with Saar Yoskovitz, an analog signal processing engineer, in 2011 founded Augury, an Israel and New York-based startup the pair describe as the “Shazam for machines.” Its wireless Halo sensors — which attach to commercial refrigerators, industrial-scale heaters, and practically everything in between — record vibration, temperature, and magnetic data and upload it to the cloud, where it is fed into AI algorithms that make predictions about the machines’ health.
Augury’s technology is engineered in such a way that it’s generalizable and improves with scale, Yoskovitz said. The recordings, which technicians take at different spots in machines, are used to establish baseline readings in Augury’s cloud. These are then compared to the sounds produced by similar appliances owned by other clients. This way, Augury doesn’t need to retrain its models for each new machine — the system over time begins to recognize abnormal sounds and other failure indicators. For example, Augury’s service might learn to spot a faulty actuator in a lifter robot and apply that knowledge to detect faulty actuators in other devices.
Early on, Augury worked directly with service companies and facility managers to diagnose critical systems, like pumps, fans, chillers, and HVAC (heating, ventilation and air conditioning) systems within commercial buildings. But it has since expanded service to noncritical machines, for which it provides continuous monitoring that’s used to provide an in-depth view of machine health, developing issues, and suggested maintenance practices.
Augury claims it’s able to reduce breakdowns by 75 percent, increase uptime by 45 percent, and lower asset costs by 30 percent by spotting the earliest signs of breakage. Technicians have used its smartphone app to save over 3,000 machines, monitor more than 60,000 industrial and commercial appliances, and avoid over 7,000 failures. In one case, Augury managed to diagnose a crack in a rotor bar that, left unchecked, would have necessitated replacing the entire motor.
To be clear, predictive maintenance solutions like Augury’s aren’t new. They’ve been used for decades in jet engines and gas turbines, and competitors like GE Digital’s Predix and startup Petasense offer similar Wi-Fi-enabled, cloud- and AI-driven vibration sensors. Some companies even perform the service in-house, like Gogo, which records in-aircraft servers’ fan speeds — an indicator of their temperature — to build decision trees for Gogo’s server operators on the ground and help predict equipment failures.
New algorithm predicts equipment failure from ultrasonic vibrations
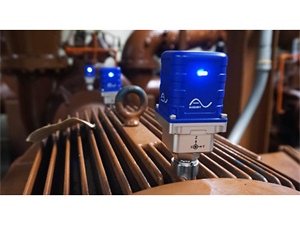
Augury’s technology is engineered in such a way that it’s generalizable and improves with scale, Yoskovitz said. The recordings, which technicians take at different spots in machines, are used to establish baseline readings in Augury’s cloud. These are then compared to the sounds produced by similar appliances owned by other clients. This way, Augury doesn’t need to retrain its models for each new machine — the system over time begins to recognize abnormal sounds and other failure indicators. For example, Augury’s service might learn to spot a faulty actuator in a lifter robot and apply that knowledge to detect faulty actuators in other devices.
Early on, Augury worked directly with service companies and facility managers to diagnose critical systems, like pumps, fans, chillers, and HVAC (heating, ventilation and air conditioning) systems within commercial buildings. But it has since expanded service to noncritical machines, for which it provides continuous monitoring that’s used to provide an in-depth view of machine health, developing issues, and suggested maintenance practices.
Augury claims it’s able to reduce breakdowns by 75 percent, increase uptime by 45 percent, and lower asset costs by 30 percent by spotting the earliest signs of breakage. Technicians have used its smartphone app to save over 3,000 machines, monitor more than 60,000 industrial and commercial appliances, and avoid over 7,000 failures. In one case, Augury managed to diagnose a crack in a rotor bar that, left unchecked, would have necessitated replacing the entire motor.
To be clear, predictive maintenance solutions like Augury’s aren’t new. They’ve been used for decades in jet engines and gas turbines, and competitors like GE Digital’s Predix and startup Petasense offer similar Wi-Fi-enabled, cloud- and AI-driven vibration sensors. Some companies even perform the service in-house, like Gogo, which records in-aircraft servers’ fan speeds — an indicator of their temperature — to build decision trees for Gogo’s server operators on the ground and help predict equipment failures.
Views: 436
©ictnews.az. All rights reserved.Similar news
- Azerbaijani project to monitor disease via mobile phones
- Innovative educational system to be improved under presidential decree
- NTRC prolongs license of two TV and radio organizations for 6 years
- Azerbaijan establishes e-registry for medicines
- Azerbaijani museum introduces e-guide
- Nar Mobile opens “Nar Dunyasi” sales and service center in Siyazan city
- International conference on custom electronic services held in Baku
- OIC secretary general to attend COMSTECH meeting in Baku
- Azerbaijan develops earthquake warning system
- New law to regulate transition to digital broadcasting in Azerbaijan
- Azerbaijani State Social Protection Fund introduces electronic digital signature
- Intellectual traffic management system in Baku to be commissioned in December
- Tax Ministry of Azerbaijan started receiving video-addresses
- World Bank recommends Azerbaijan to speed up e-service introduction in real estate
- Azerbaijan to shift to electronic registration of real estate