



Date:07/01/20
The next big thing in 3D printing just might be so-called "4D materials" that employ the same manufacturing technique but are designed to deform over time in response to changes in the environment, like humidity and temperature. They're also sometimes known as active origami or shape-morphing systems. MIT scientists successfully created flat structures that can transform into much more complicated structures than had previously been achieved, including a human face. They published their results last fall in the Proceedings of the National Academy of Sciences.
Prior researchers had successfully come up with ways to get such materials to shape-shift into simple structures. MIT mechanical engineer Wim van Rees, a co-author of the PNAS paper, devised a theoretical method to turn a thin, flat sheet into more complex shapes, like spheres, domes, or a human face. "My goal was to start with a complex 3-D shape that we want to achieve, like a human face, and then ask, 'How do we program a material so it gets there?'" he said. "That's a problem of inverse design."
But his original simulations were for an idealized sheet of material with no boundaries on how much it could expand or contract, and most real-world materials do have limits. It's a problem of "double curvature," first described by 19th century mathematician Carl Friedrich Gauss.
Gauss proposed his "Therema Egregium" (remarkable theorem) in 1828, which holds that one can determine the curvature of a surface just by measuring its angles and distances. That means that the surface curvature doesn't change when you bend it—say, by folding a slice of delicious pizza in order to eat it with minimal mess, since the folding makes the slice more rigid in the direction perpendicular to the fold. It's also the secret behind the strength of corrugated boxes, as well as Pringle's brand potato chips, and why scientists were able to figure out that the universe is flat.
But there's a caveat: the surface can't stretch, shrink, or tear, which poses a problem when you're trying to deform a flat sheet into intricate shapes with a different Gaussian curvature. Van Rees likened the challenge he faced to trying to gift-wrap a soccer ball. The paper has zero Gaussian curvature, while the ball has double curvature. So in order to wrap the soccer ball, you have to crease and crumple the paper at the sides and bottom; the paper would have to stretch or contract in all the right places.
To address this issue, van Rees and his colleagues decided to use a mesh-like lattice structure instead of the continuous sheet modeled in the initial simulations. They made the lattice out of a rubbery material that expands when the temperature increases. The gaps in the lattice make it easier for the material to adapt to especially large changes in its surface area. The MIT team used an image of Gauss to create a virtual map of how much the flat surface would have to bend to reconfigure into a face. Then they devised an algorithm to translate that into the right pattern of ribs in the lattice.
They designed the ribs to grow at different rates across the mesh sheet, each one able to bend sufficiently to take on the shape of a nose or an eye socket. The printed lattice was cured in a hot oven, and then cooled to room temperature in a saltwater bath. And voila! It morphed into a human face. The team also made a lattice containing conductive liquid metal that transformed into an active antenna, with a resonance frequency that changes as it deforms.
These kinds of shape-shifting materials might one day be used to make tents that can unfold and inflate on their own, just by changing the temperature (or other ambient conditions). Other potential uses include deformable telescope lenses, stents, scaffolding for artificial tissue, and soft robotics.
"I'd like to see this incorporated in, for example, a robotic jellyfish that changes shape to swim as we put it in water," said van Rees. "If you could use this as an actuator, like an artificial muscle, the actuator could be any arbitrary shape that transforms into another arbitrary shape. Then you're entering an entirely new design space in soft robotics."
MIT scientists made a shape-shifting material that morphs into a human face
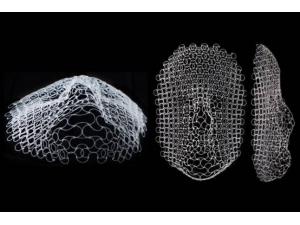
Prior researchers had successfully come up with ways to get such materials to shape-shift into simple structures. MIT mechanical engineer Wim van Rees, a co-author of the PNAS paper, devised a theoretical method to turn a thin, flat sheet into more complex shapes, like spheres, domes, or a human face. "My goal was to start with a complex 3-D shape that we want to achieve, like a human face, and then ask, 'How do we program a material so it gets there?'" he said. "That's a problem of inverse design."
But his original simulations were for an idealized sheet of material with no boundaries on how much it could expand or contract, and most real-world materials do have limits. It's a problem of "double curvature," first described by 19th century mathematician Carl Friedrich Gauss.
Gauss proposed his "Therema Egregium" (remarkable theorem) in 1828, which holds that one can determine the curvature of a surface just by measuring its angles and distances. That means that the surface curvature doesn't change when you bend it—say, by folding a slice of delicious pizza in order to eat it with minimal mess, since the folding makes the slice more rigid in the direction perpendicular to the fold. It's also the secret behind the strength of corrugated boxes, as well as Pringle's brand potato chips, and why scientists were able to figure out that the universe is flat.
But there's a caveat: the surface can't stretch, shrink, or tear, which poses a problem when you're trying to deform a flat sheet into intricate shapes with a different Gaussian curvature. Van Rees likened the challenge he faced to trying to gift-wrap a soccer ball. The paper has zero Gaussian curvature, while the ball has double curvature. So in order to wrap the soccer ball, you have to crease and crumple the paper at the sides and bottom; the paper would have to stretch or contract in all the right places.
To address this issue, van Rees and his colleagues decided to use a mesh-like lattice structure instead of the continuous sheet modeled in the initial simulations. They made the lattice out of a rubbery material that expands when the temperature increases. The gaps in the lattice make it easier for the material to adapt to especially large changes in its surface area. The MIT team used an image of Gauss to create a virtual map of how much the flat surface would have to bend to reconfigure into a face. Then they devised an algorithm to translate that into the right pattern of ribs in the lattice.
They designed the ribs to grow at different rates across the mesh sheet, each one able to bend sufficiently to take on the shape of a nose or an eye socket. The printed lattice was cured in a hot oven, and then cooled to room temperature in a saltwater bath. And voila! It morphed into a human face. The team also made a lattice containing conductive liquid metal that transformed into an active antenna, with a resonance frequency that changes as it deforms.
These kinds of shape-shifting materials might one day be used to make tents that can unfold and inflate on their own, just by changing the temperature (or other ambient conditions). Other potential uses include deformable telescope lenses, stents, scaffolding for artificial tissue, and soft robotics.
"I'd like to see this incorporated in, for example, a robotic jellyfish that changes shape to swim as we put it in water," said van Rees. "If you could use this as an actuator, like an artificial muscle, the actuator could be any arbitrary shape that transforms into another arbitrary shape. Then you're entering an entirely new design space in soft robotics."
Views: 569
©ictnews.az. All rights reserved.Similar news
- Azerbaijani project to monitor disease via mobile phones
- Innovative educational system to be improved under presidential decree
- NTRC prolongs license of two TV and radio organizations for 6 years
- Azerbaijan establishes e-registry for medicines
- Azerbaijani museum introduces e-guide
- Nar Mobile opens “Nar Dunyasi” sales and service center in Siyazan city
- International conference on custom electronic services held in Baku
- OIC secretary general to attend COMSTECH meeting in Baku
- Azerbaijan develops earthquake warning system
- New law to regulate transition to digital broadcasting in Azerbaijan
- Azerbaijani State Social Protection Fund introduces electronic digital signature
- Intellectual traffic management system in Baku to be commissioned in December
- Tax Ministry of Azerbaijan started receiving video-addresses
- World Bank recommends Azerbaijan to speed up e-service introduction in real estate
- Azerbaijan to shift to electronic registration of real estate